About me
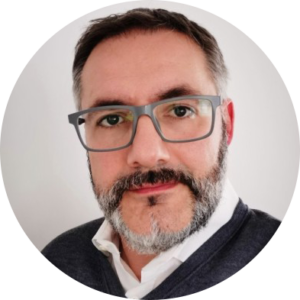
B.Sc. Computer Science Engineering, 24 years of working experience, 18 of which was in the Automotive industry, primarily in the domain of Quality, Operations, and Development.
My years of experience has resulted in strong ability to evaluate technical aspects, quality, and economical constraints in every industrial context, in addition to a solid negotiating competence.
I am prepared, I am a quick learner and I follow rigorous methodology.
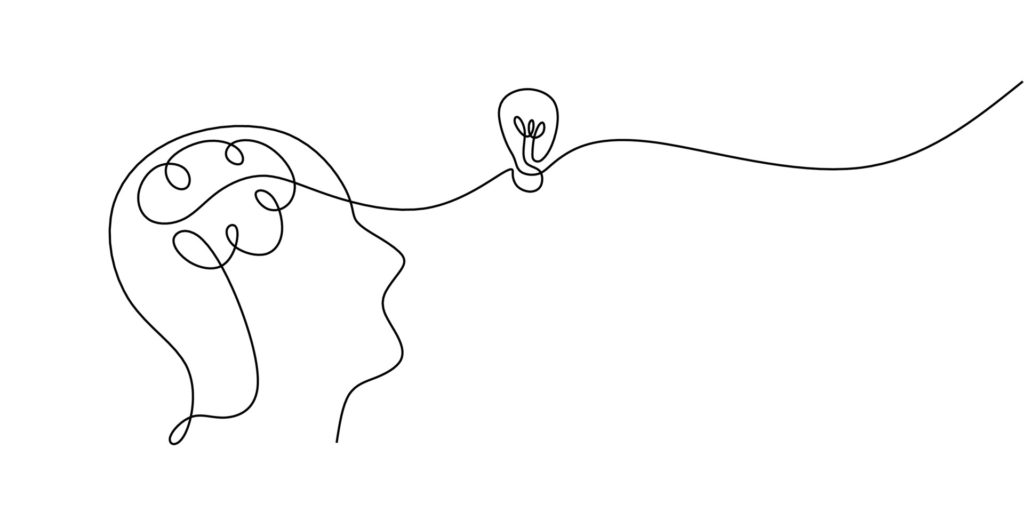
I love challenges, I have a lot of experience in Change Management, and I am oriented towards a structural result that is maintained over time.
The experiences gained in my professional roles allow me fully prepared when approaching various areas. I like to work with people I can learn from, and who challenge my skills.
My career path
I began my career as a graduate SW and industrial automation developer on MCM systems, then extended my role to full management of the automation line according to customer requirements.
During those years (2003-2006) I often travelled to client facilities (15 months in the USA at Metaldyne, 6 months in France at Dassault, and 4 months in Germany at EADS).
I was able to learn to manage projects and teams, as well as the culture of the country where I lived.
At the end of 2006 I joined Ferrari’s team, where I worked for 8 years. Initially oversaw the new engine’s industrialization (in the Manufacturing CNC Facility first, at the Assembly and Test line later on).
During these 4 years I worked closely with Technical Department and Purchasing, and I also experienced Production and Quality.
In 2010 I was asked to join the Purchasing Department team, as RPA (Project Manager): I managed the team of buyers for the powertrain commodity, I supervised important suppliers and acquired increasing responsibilities, to where I managed a purchasing budget of € 55M and the responsibility of 8 resources.
I worked closely with the Technical team on the final development and industrialization of the PTU (4WD gearbox installed on the Ferrari FF): it was a challenging project, both in terms of performance and timing constrains. It was the first time that a double gearbox was fitted on a Ferrari car.
I worked on a small team (4 people) and I was responsible for the technology and purchasing perimeter.
The project enthralled me, and was a great success, so I was asked to join the new team on the 8-cylinder car, in the Development Department (for the Ferrari California 30).
As a Program Manager, I followed all the activities, KPI indicators, and reports of project progress in the development area. This experience allowed me to gain great experience in managing a complete car project.
This experience, in direct contact with the style, development and testing team allowed me to complete my knowledge of the processes related to the development of a complete car and also to assist in the creation of a fantastic product, where the maniacal attention to details and performance reaches levels of absolute excellence.
After this experience I was asked to return to the Purchasing Department, no longer to coordinate buyers, but to manage the rising problems concerning the supplier product in development (which were rising due to the crisis of 2008), working together with the Supplier Quality.
Thanks to my previous experience and technical skills in production, industrialization, and tooling I was able to support the Purchasing dept. in difficult situations, including collaboration with international suppliers.
In 2014 I left Ferrari to begin an experience on my own as a consultant, because I wanted to straighten out complicated situations in other areas. One of the first important projects happened to be with the company FOM Tacconi and involved a possible opening towards companies in the Chinese market. Little by little I was engaged by the Group, which eventually hired me to lead the group’s technological assets.
As Group Technology Director, I managed n.4 production facilities, I was well traveled (Germany, Romania, Holland, France, Austria).
I also dealt with main customer and important economical deals for new production lines. During this period, I was able to recover a few troubled businesses, making them fully profitable.
The group, with my help overcame a difficult period, leading them to request that I also support the sales Dept. for some important customers.
I was very pleased; however, a part of me missed the consultancy projects. So, after an extremely rewarding and intense experience with FOM Tacconi, I decided to leave the position and follow my passions.
2015 – Freelancing
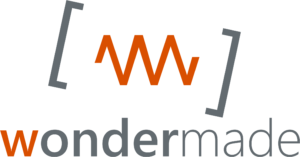
Freelancing provided me the opportunity to take new challenges in different sectors, new to my prior experience.
I enjoyed working in new sectors, exploring the possibilities that the new environments could have to use some of my skills for the community I belonged.
Some of the main activities I worked on include:
- Product Development Manager (Air Quality IoT device – Segantini)
- Lead Interaction Designer (Interactive projection table – IAT)
- Contract Professor (2 digital technology classes – ITS Reggio Emilia)
- Interaction Designer (speaking plane engine – Spazio Gerra)
- Product Development of a new HMI (Biomedical device, Mantis Italia)
Other activities with private companies and public institutions.
I joined LAM in 2015, at the very beginning with a very specific mandate to introduce a new production line in the company. The project started as technical support for the launch of a new production technology, and since then evolved into a broader project, targeted to reorganize the processes of the entire company.
Soon, I was offered the position of Quality Director, with the goal to restructure the quality Team, consolidate the ISO 9001 certification, and prepare for the IATF certification path. Since the company was new, small, and lacking the history of working with many OEMs in the Automotive sector these tasks were not simple.
Working together with the CEO and General Management, we were able to double the income, increase the team, and create more robust internal processes which all allowed for the company to obtain the IATF certification in 2016.
As a temporary manager my goal was also to create a new Quality team and train a new leader. To free myself and support the Management in relations with the most important customers, and of course in the implementation of internal processes in order to increase efficiency and profitability.
During the period 2015-2019 I worked closely with the Technical Department and Purchasing, and I helped expand the company that now has a new warehouse facility and a completely new layout, organization, and material flow.
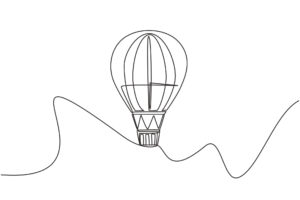
I moved to Montreal at the end of 2019, embracing a new chapter of my life with my family.
Why Canada? I am asked this question a lot.
Canada is one of the world’s most multicultural countries: I believe that the diversity of Canada’s population has helped to make Canadian residents very welcoming to new arrivals. Canada current cultural orientation is very inclusive, open and friendly; welfare is highly developed, job openings are very compatible with our skills and background.
On top of that, Canada was ranked in 2021 the best overall Country! (here)
I joined Dana TM4 in March 2020; my responsibilities included defining the vision, strategies, direction, and objectives of quality service for all Dana TM4 activities.
I was also responsible for optimizing and implementing the company’s ISO processes up to the IATF16949 standard implementation.
I was the key person in leading the Automotive internal transformation related to Quality and Operation.
I acted as lead auditor for the working environment to ensure compliance with all quality standards were met and I was responsible in solving quality complaints submitted from the manufacturing floor, prototype build events, customers, and vendors.
I joined Taiga Motors’ Team in October, as Supply Chain and Quality Director, embracing the dynamic environment that a accompanies a start-up during the early stages.
Reporting to the COO, I was fully responsible for strategic sourcing, material planning, supplier qualification, delivery, quality inspection, storing, distribution, and final assembly of Taiga vehicles.
One big challenge was creating the Supply Chain and Quality processes and team: I was directly involved in all the process definition and implementation, all the hiring process, the ERP/MRP implementation, Supplier base creation, contract management, all logistic aspects, and international freights.
On a quality side the main priority was to help the RnD Department define the correct quality needs during the product development and ensure those are met in qualification and production.
Alfiere Innovation is born! And it is a beginning of a new chapter for me.
As a Senior manager for different companies in my career experiences, my energy, analytic skills, organizational abilities, and creativity in tackling problems have made positive contribution.
I am equally comfortable working independently to meet company goals, as well as collaboratively as part of a team. I have always been able to establish and maintain excellent relationships with clients and coworkers at all levels.
Since 2015, I am a volunteer for the Italian Foundation BET SHE CAN (no-profit organization promoting pre-teen girls empowerment) as Technology consultant, as trainer on STEM workshops, as Technical advisor on proposals, which is also enriching my social experience and really giving me back a lot more than I provide.
Curious? www.betshecan.org